Blog
Thermoforming Design Series: Material Selection, Process Optimization, and Quality Control
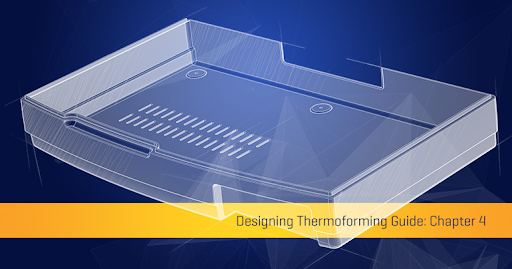
Introduction
Thermoforming has become a cornerstone of modern manufacturing, producing everything from automotive panels and medical trays to food containers and industrial housings. However, achieving consistent quality, cost efficiency, and performance in thermoforming requires more than just heating and shaping plastic—it demands careful material selection, precise process control, and rigorous quality assurance.
Choosing the right thermoplastic, optimizing forming efficiency, and implementing strict quality control measures can reduce defects, minimize waste, and improve part performance. This article explores the science of material selection, the strategies for optimizing forming efficiency, and the quality control techniques that ensure high-performance thermoformed parts.
1. Material Selection: The Foundation of Successful Thermoforming
Selecting the right thermoplastic is critical for determining a product’s durability, flexibility, heat resistance, and chemical stability. The wrong material choice can result in brittle parts, excessive warping, or poor surface quality, leading to costly redesigns and manufacturing inefficiencies.
1.1 Key Factors in Thermoplastic Selection
Not all plastics behave the same during thermoforming. Each material has unique mechanical, chemical, and aesthetic properties that impact its performance.
Factor | Considerations | Common Materials |
Rigidity vs. Flexibility | Some applications require rigid plastics for structural strength, while others need flexible materials for impact absorption. | Rigid: HIPS, ABS, PC Flexible: LDPE, PP |
Transparency vs. Opacity | Transparent materials are used for clear packaging and medical trays, while opaque plastics offer enhanced durability. | Transparent: PETG, PC, Acrylic Opaque: ABS, HIPS, Kydex |
Chemical & Heat Resistance | Materials must withstand chemicals, UV exposure, and extreme temperatures. | Heat Resistant: PC, PP, Kydex Chemical Resistant: PE, PP, PVC |
Food Safety | FDA-approved materials must be used for food and medical applications. | Food-Safe: PETG, PP, HIPS |
1.2 Common Thermoforming Materials and Their Applications
- High-Impact Polystyrene (HIPS): Cost-effective, lightweight, and easy to form, making it ideal for packaging trays and lightweight structural components.
- PETG (Polyethylene Terephthalate Glycol-Modified): Excellent clarity and impact resistance, perfect for food-safe packaging and medical trays.
- ABS (Acrylonitrile Butadiene Styrene): High impact strength and chemical resistance, commonly used for automotive parts and protective covers.
- Polycarbonate (PC): High stiffness and temperature resistance, ideal for protective shields and medical equipment.
- Polyethylene (PE – HDPE/LDPE): High chemical resistance and flexibility, widely used for containers, liners, and trays.
- Polypropylene (PP): Superior chemical resistance and thermal stability, commonly found in lab equipment and food containers.
1.3 Custom Material Runs: Reducing Waste and Costs
Ordering custom sheet sizes minimizes scrap rates and material waste, reducing overall costs. Most suppliers offer custom orders for high-volume runs, with minimum order quantities ranging from 500 to 5,000 lbs.
1.4 Optimizing Material Usage
Material costs contribute significantly to production expenses. To reduce waste, manufacturers should:
✔ Optimize part nesting to maximize sheet usage.
✔ Select the right stock size to minimize excess trimming.
✔ Use multi-up tooling to form multiple parts per sheet.
Choosing the right material from the start ensures better performance, lower costs, and fewer production issues.
2. Optimizing Thermoforming Efficiency: Strategies for Cost-Effective Production
Efficiency in thermoforming is determined by draw ratios, tooling design, and process control. A poorly optimized process results in excessive material thinning, increased defects, and wasted resources.
2.1 Understanding Draw Ratios
The draw ratio defines how much a plastic sheet stretches during forming:
Draw Ratio=Part Depth (Z)Minimum Width (X) or Length (Y)\text{Draw Ratio} = \frac{\text{Part Depth (Z)}}{\text{Minimum Width (X) or Length (Y)}}Draw Ratio=Minimum Width (X) or Length (Y)Part Depth (Z)
Draw Ratio | Effect on Material |
1:1 or lower | Uniform thickness, minimal thinning |
4:3 | Maximum recommended for standard thermoforming |
Above 4:3 | Excessive thinning, weak spots, potential defects |
If a part’s design exceeds the recommended draw ratio, manufacturers should:
✔ Increase the initial sheet thickness to compensate for stretching.
✔ Use plug assists to pre-stretch material evenly and prevent defects.
2.2 Plug Assists: Controlling Material Flow
Plug assists are mechanical tools that pre-stretch plastic before final forming, ensuring:
✅ Uniform thickness distribution
✅ Prevention of material bunching and webbing
✅ Improved surface detail
Plug assists are especially useful for deep-draw parts and complex geometries.
2.3 Multi-Up Tooling: Maximizing Output and Reducing Labor Costs
By forming multiple parts per sheet, manufacturers can increase efficiency and lower costs.
Tooling Setup | Parts Per Cycle | Efficiency Gain |
1-up Tooling | 1 | Best for prototyping and low-volume production |
4-up Tooling | 4 | Cuts labor costs by 75% |
8-up Tooling | 8 | Maximizes efficiency for high-volume production |
For example, if a machine processes 5 sheets per hour, a 4-up tool produces 20 parts per hour, compared to just 5 parts per hour with a 1-up tool.
Optimizing forming efficiency reduces production time, labor, and material costs, ensuring greater profitability.
3. Quality Control: Ensuring Precision and Consistency
Even with optimized material selection and forming efficiency, inconsistent shrinkage, thickness variation, and defects can impact thermoformed parts. Implementing quality control measures ensures precision, repeatability, and reliability.
3.1 Thermoforming Tolerance Guidelines
Thermoformed parts have looser tolerances than machined or injection-molded parts.
Feature | Tolerance (inches) |
Formed Measurements (<6″) | ±0.015” |
Medium Parts (6–12″) | ±0.025” |
Large Parts (>18″) | ±0.030” + 0.002”/inch |
By considering material shrinkage, trimming accuracy, and mold precision, manufacturers can maintain consistent part quality.
3.2 Common Thermoforming Defects & Solutions
Defect | Cause | Solution |
Excessive Thinning | High draw ratio, sharp corners | Use plug assists, reduce draw depth |
Webbing (Material Bunching) | Poor mold design, excessive stretching | Adjust mold design, improve material flow |
Warping | Uneven cooling, internal stress | Improve cooling uniformity, adjust mold temperature |
3.3 In-Process Quality Monitoring
✔ Thickness measurements at critical points ensure material distribution is within tolerance.
✔ Mold fit checks confirm proper material shrinkage control.
✔ CNC trimming verification guarantees edge accuracy and hole placement.
Thermoforming Success Starts with the Right Process
Thermoforming remains one of the most efficient and scalable manufacturing processes for plastic components, but success requires careful material selection, optimized forming strategies, and rigorous quality control.
Get Expert Thermoforming Solutions with RapidMade
At RapidMade, we specialize in custom thermoforming solutions, offering:
✅ Expert guidance on material selection
✅ Precision CNC trimming and finishing
✅ High-volume production efficiency
📞 Contact us today to optimize your thermoforming process!
📩 Email: [email protected]
🌐 Website: rapidmade.com
With RapidMade’s expertise, you can achieve cost-effective, high-quality thermoformed parts—built to perform.
-
Fashion8 months ago
LiteroticaTags Explained: Find And Use The Top Tags For 2025
-
BUSINESS9 months ago
What is NippyDrive? A Complete Guide to Using NippyDrive
-
Biography8 months ago
Coco Lovelock Bio, Age, Career, Net Worth, Height, Education, Boyfriend & More
-
Biography8 months ago
Who Is Meow Miu? Get to Know the Latest Star in the Spotlight
-
Fashion8 months ago
Webfreen.com Fashion: Redefining Affordable Luxury
-
Home Improvement8 months ago
Valvula Check 32mm Sodimac: Comprehensive Guide
-
TECHNOLOGY6 months ago
Transform Text into Stunning Videos: Free Online AI Text-to-Video Generator
-
BUSINESS6 months ago
9 Packaging Trends You Can’t Afford to Ignore in 2025